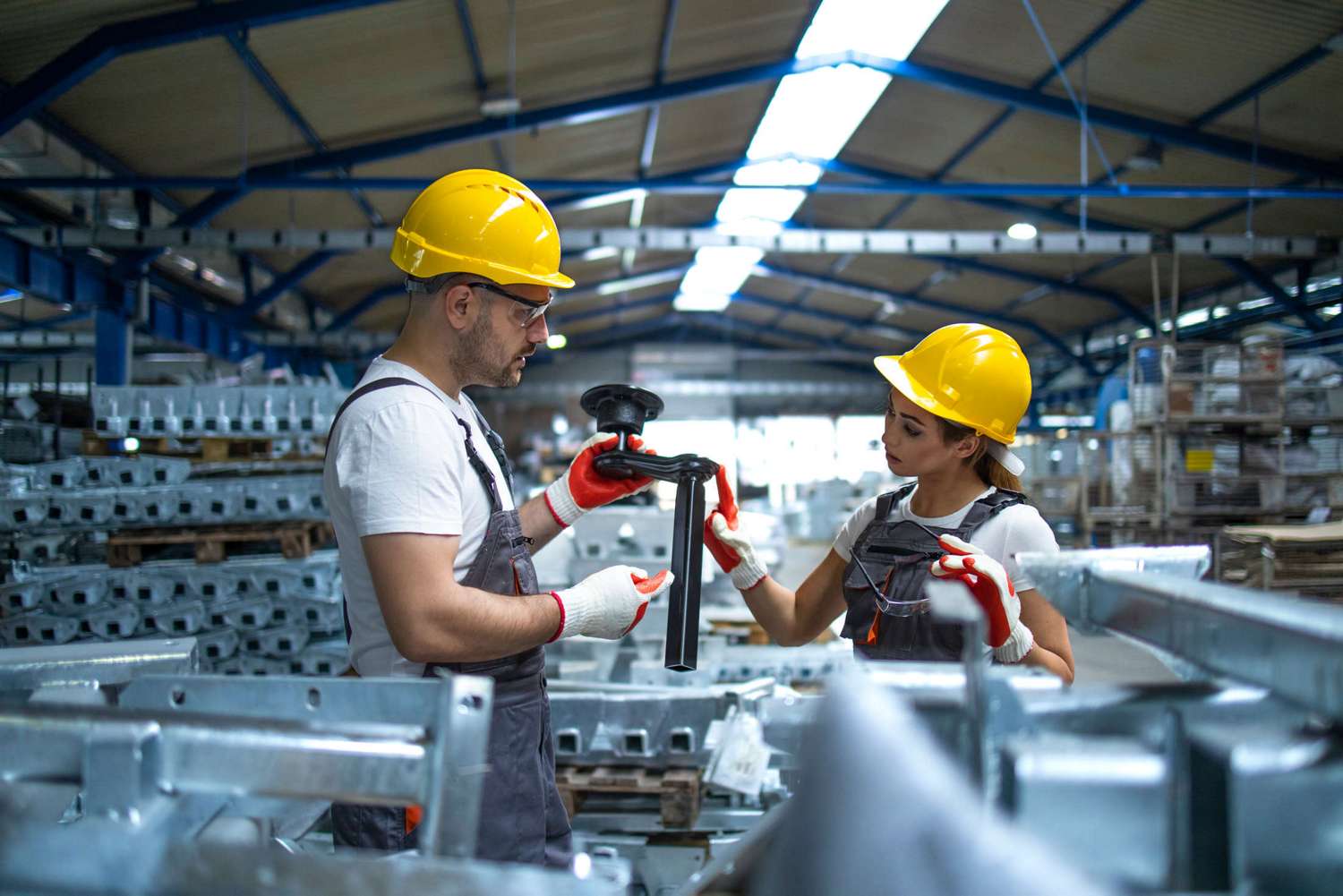
PVC or PUR: How to Choose the Right Cable Jacket
Cables are an essential part of any industrial application. Ensuring the cables are properly protected in various industrial environments is also critical, and the first line of defense is the cable jacket. The cable jacket is the outermost layer of a cable that protects the insulation and conductor from external damage. Choosing the appropriate cable jacket material for the environment, especially where chemical cleaning solutions, cutting fluids, and other caustic liquids are present, will increase cable lifespan and increase overall uptime.
Comparing Cable Jacket Materials
Two common types of cable jacket materials used in industrial applications are PVC and PUR. Both of these materials are flexible and durable thermoplastics, materials which melt at extremely high temperatures and become solid again when cooled. Even though they are both plastics, their differing physical properties imbues them with unique abilities. These abilities make PVC cables and PUR cables suited for use in different types of environments.
Polyvinyl chloride, or PVC, is a widely used, general-purpose cable jacket material due to its versatility and low cost. PVC cables can resist heat, oils, moisture, and abrasions, but are especially resistant to common cleaning chemicals. Polyurethane, known as PUR, is also good for oil, moisture, and abrasion resistance, but does not have the same heat resistance qualities as PVC. However, PUR cables are stronger and more flexible.
PVC Cables and When to Use Them
PVC cable jackets are inherently flame- and heat-resistant, owing to their chemical makeup. They can also resist oils, acids, abrasions, sunlight, salt water, ozone, oxidation, and moisture, and a PVC cable with an IP69K rating means it is sealed against the ingress of water even during washdown. This makes them an excellent choice for most chemical washdown applications in the food industry and beverage industry. Because PVC is a blend of materials and can vary from manufacturer to manufacturer, its properties can be adjusted and tailored for specific applications and conditions. PVC cable jackets have good-to-excellent resistance to common cleaning solvents including, but not limited to:
- sodium hypochlorite
- sodium hydroxide
- potassium hydroxide
- peracetic acid
- hydrogen peroxide
- quaternary ammonium compounds
You will find PVC cable jackets in other applications across many different industries, including packaging and assembly lines, lighting, and medical manufacturing.
When choosing a cable jacket material, it is also important to consider the concentration of chemicals, temperature of the process, and the duration and frequency of exposure since these factors can impact the suitability of PVC for these applications. For example, though PVC has some resistance to oils, other materials such as PUR offer improved oil resistance, making PVC less suited for automotive and machine tool industries.
In addition to cleaning chemical resistance, PVC cables are typically more rigid than other types of cables. This makes them suitable for use in applications where they will be exposed to high temperature, high pressure washdown. The rigidity of the PVC sheathing protects the cable from damage and extends the life of the cable. However, the rigidity of PVC cables can be a disadvantage in freezer applications, where low temperatures can cause the material to crack if the cables are being flexed.
Condition | PVC Cable | PUR Cable |
Cleaning Chemicals | ✓ | |
Washdown Applications | ✓ | |
Cutting Fluids/Oils | ✓ | |
Repeated Flexing | ✓ |
PUR Cables and When to Use Them
Like PVC, PUR is a thermoplastic material used for cable jackets. However, the chemical composition of polyurethane is noticeably different than that of polyvinyl chloride. Despite not having the natural fire resistance of PVC, PUR does not contain halogens like PVC does and will not emit toxic fumes if exposed to fire. It also creates little smoke. This makes PUR the preferred material in the European Union because EU regulations required “low/no smoke, low/no halogen” properties to be identified on the cable jacket. In case of an incident, fewer halogens will be released into the air.
PUR cables have a high tensile strength and are resistant to UV light, water, tears, and abrasions. They are also resistant to weld slag, cutting fluids, oils, solvents, and other harsh chemicals, making them a good choice for many automotive manufacturing, stamping, and machining applications.
One standout feature of PUR cables is their flexibility and small bend radius. This makes them ideal for applications where connections move or bend frequently, such as robotic applications. Many PUR cables can maintain flexibility even in low temperatures. Besides robotics, PUR cables’ flexibility lends itself to use in paint facilities, medical applications, and other applications with constant movement.
Contact Banner for Help Choosing Your Cable Jacket
With the different advantages PVC and PUR cables have, be sure you are getting the best option for your specific application by talking about it with a Banner expert today.