Small Motor Condition Monitoring & Predictive Maintenance
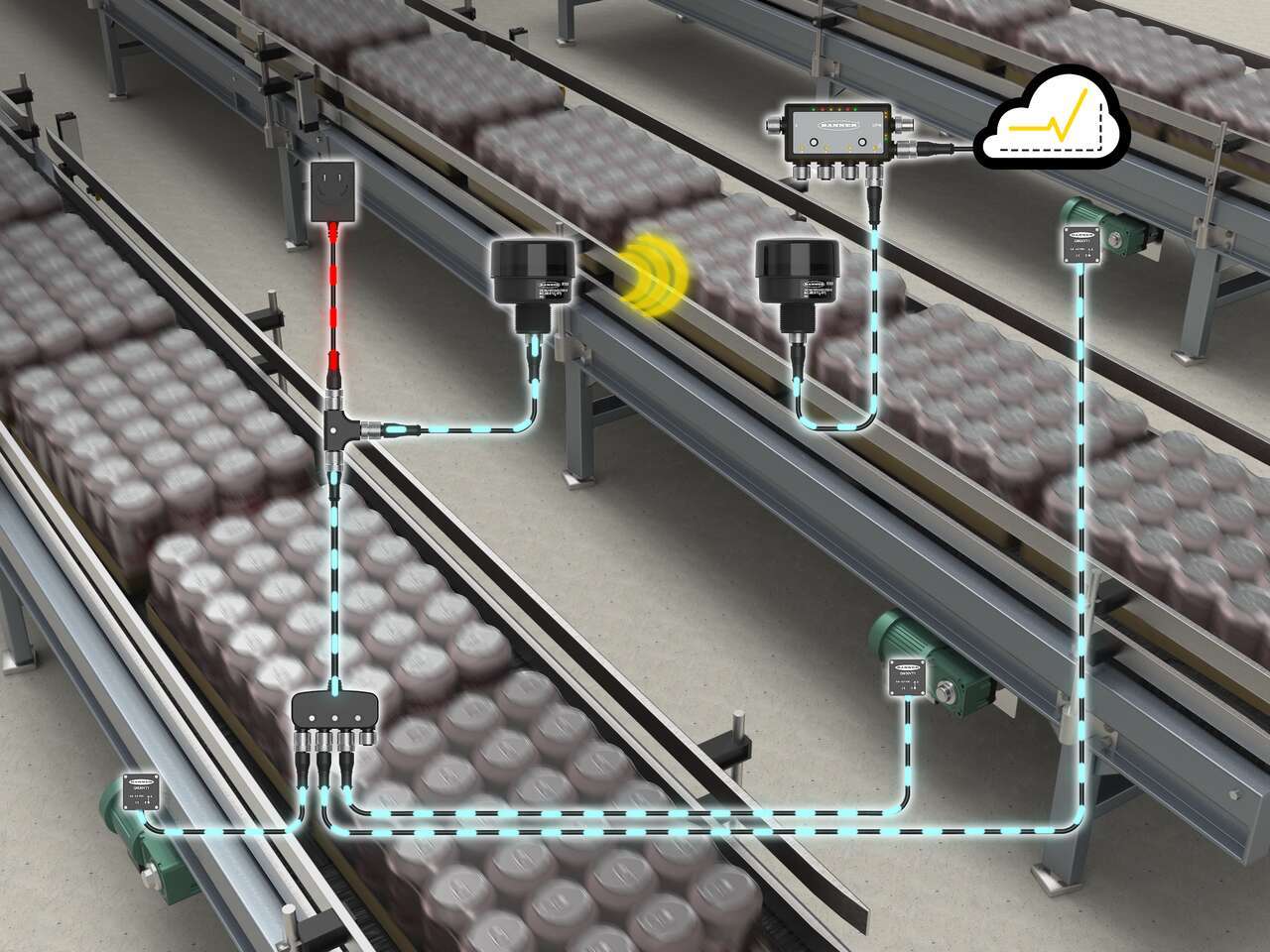
Challenge: Catch declining conveyor motor performance before failure
A beverage manufacturer was experiencing production loss due to occasional unexpected conveyor motor failures in various parts of the plant. Plant management decided to examine one production line to catch declining motor performance and reduce failures that trigger unexpected production shutdowns.
Solution: Condition Monitoring with Snap Signal
To test predictive maintenance on one of the production lines, management decided to install a monitoring system composed of a Banner DXMR90 controller, Vibe-IQ vibration analysis script, and four QM30VT2 vibration and temperature sensors. This included a sensor for each of the four conveyor motors on the line. Vibe-IQ detects gradually declining motor performance to catch problems before failures occur. It can catch motor temperature rise and unusual vibrations, such as those caused by worn bearings, loose motor mounts, or a slipping belt. After the monitoring system was installed and operating for a few weeks, it began detecting excessive heat and vibration in one of the motors and displayed this data on a motor-condition dashboard via Banner Cloud Data Services (CDS). The maintenance group was able to inspect the motor during a planned shutdown, and it found the bearings had excessive wear. It installed a new motor during the shutdown and was able to ensure the line was functional when it was scheduled to be running again. After this trial, the plant manager installed monitoring systems on two more lines and made plans to install them on the remaining three lines over the following three months.
Key Benefits
ALLOWS USERS TO START SMALL AND SCALE FAST
The DXMR90 with Vibe-IQ vibration analysis script simplifies and streamlines the deployment of IIoT solutions into a plant. Cost-effective and easy to install, the system will begin collecting data immediately as part of a 24-hour baseline, after which it will begin displaying a motor-condition dashboard (via Cloud Data Services). Banner’s condition monitoring system includes sensors for the most common applications. After the system is installed and collecting data, the process of growing the solution is as simple as adding more sensors directly, or by adding R70SR9MQ serial data radios for wireless communication from additional remote devices.
OFFERS COMPLETE, END-TO-END IIOT SOLUTIONS
The DXMR90 with Vibe- IQ uses a patented machine-learning algorithm to baseline all connected sensors right out of the box. The system sets values and control limits for alerts and warnings for each motor, and it requires minimal user interaction. The Banner Cloud Data Services (CDS) platform provides powerful tools that make it easy to visualize and analyze data from each device in the network for direct-to-cloud functionality on the first day. The system allows facilities to get up and running and collect valuable data in minutes, not hours.
MAXIMIZE UPTIME AND INCREASE EFFICIENCY
Condition monitoring for predictive maintenance is a key capability of Banner’s Snap Signal product portfolio. The CDS platform allows users to view, store, protect, and export critical data collected by wired and wireless sensors. Device data is actionable, making it easy to identify trends, predict maintenance requirements, avoid costly equipment failures, and prevent unplanned downtime.
MAKE BETTER DATA-DRIVEN DECISIONS
The Cloud Data Services platform is more than a dashboard. With analytics and visualization tools, the software delivers actionable insights that allow users to solve real challenges in their facility. Machine learning resides in the configuration files of the DXM controller, which integrates with CDS to generate the dashboards that display asset condition. In addition, the ability to store data and analyze trends over time helps users make better, data-driven decisions for the long-term.