Tray Denesting Solutions for Food Packaging
The denester machine is responsible for initiating the start of food trays and containers traveling down the conveyor. The denester removes single trays from the magazine and places each tray onto the packaging line in the proper orientation. The trays are then transported into the filling area via conveyor.
High-performing denesters are important because they are the first stage where a company can work to increase efficiency throughout the entire food packaging line. Production rates can only increase as fast as containers can be moved onto the line, so it is especially important to use reliable sensors for maximum productivity and profitability. Any jams or slowdowns at this point can negatively affect performance further down the food packaging line.
Tray detection during the infeeding stage can present different challenges. Solutions are needed that can monitor stack levels and alert operators when refills are needed, as well as detect trays to ensure that they are placed on the conveyor one at a time and at the proper spacing.
Food trays can be made with different materials or colors which can affect accurate detection. For instance, clear plastic containers present a unique challenge for most photoelectric sensors. Fortunately Banner offers various products suitable for recognizing transparent objects such as the Q4X Series Sensor and the QS18 Expert™ Clear Object Detection Sensor. There are also other laser-based sensor options that can detect dark colored trays and even those made of foil, both of which are typically used for pre-packaged foods.
Featured Applications
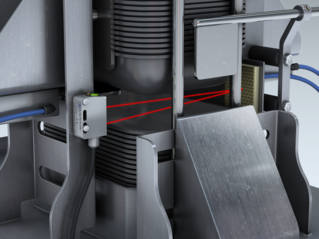
Monitoring Plastic Tray Levels on a Denester Machine
Tracking tray levels on a denester machine ensures that product is replenished in a timely manner and does not affect production.
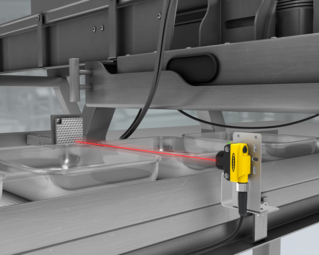
Controlling Line Pressure of Clear Food Trays at Denester
Using a sensor in clear object sensing mode to ensure proper staging of plastic trays during denesting process.