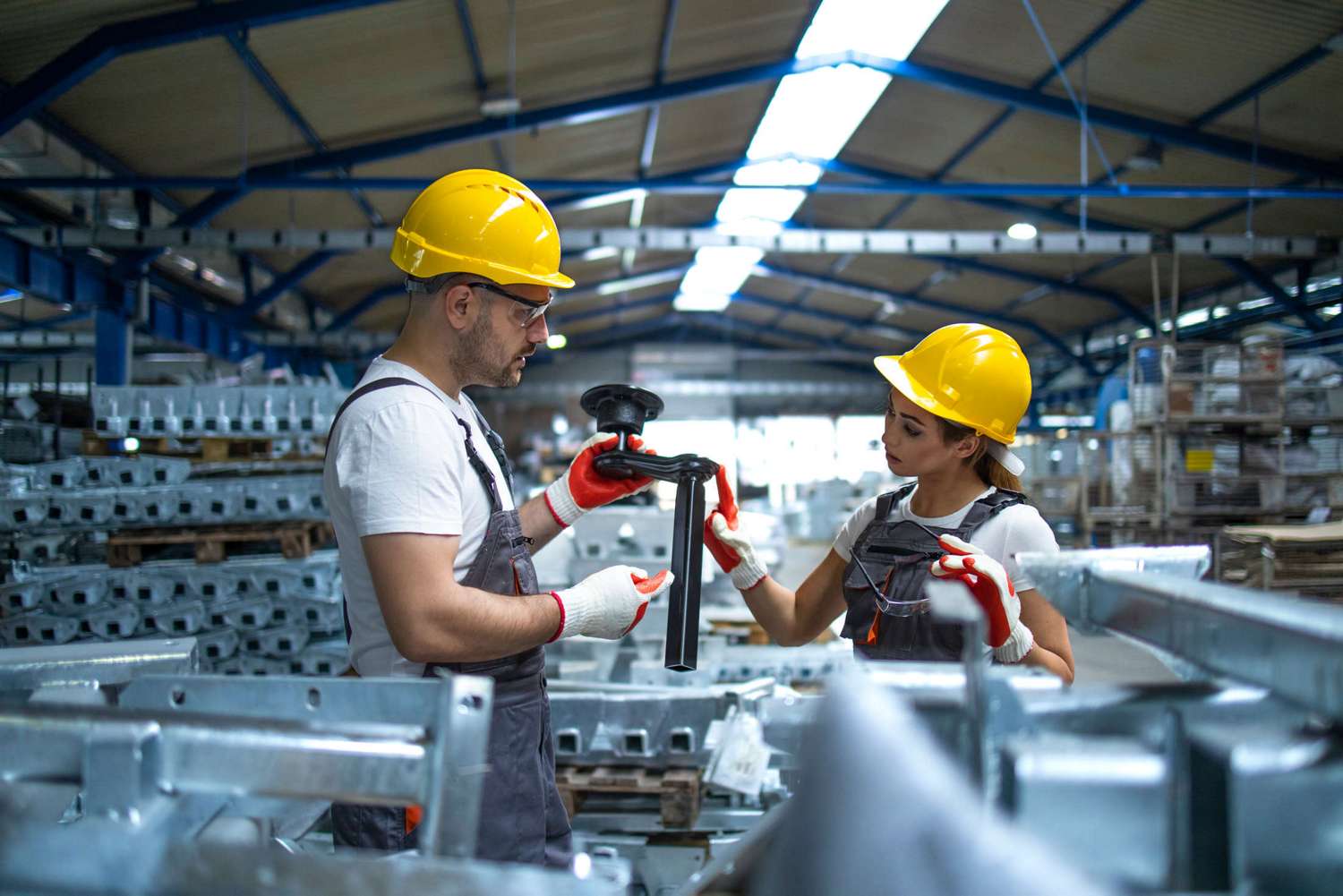
Ultrasonic Sensors 101: Answers to Your Frequently Asked Questions
There are many different types of technologies sensors use to detect and measure in industrial settings, including laser and radar. Unlike these others which use varying portions of the light spectrum, ultrasonic sensors use sound. Each technology works well for different applications, so let’s explore how ultrasonic sensors work.
What Is an Ultrasonic Sensor?
Ultrasonic sensors are devices that generate ultra-high-frequency sound waves greater than 20 kHz, beyond the range of human hearing. They use electrical energy and a ceramic transducer, which both transmits and receives sound waves. Sound waves are essentially pressure waves that travel through solids, liquids and gases and can be used in industrial applications to measure distance or detect the presence or absence of targets.
How Does an Ultrasonic Sensor Work?
The sensor has a ceramic transducer that vibrates when electrical energy is applied to it. The vibrations compress and expand air molecules in waves that travel from the sensor face to a target object. The ultrasonic sensor measures distance by emitting a sound wave and then "listening" for a set period of time, allowing for the return echo of the sound wave bouncing off the target, before retransmitting.
When Would I Use an Ultrasonic Sensor?
Because ultrasonic sensors use sound rather than light for detection, they work in applications where photoelectric sensors may not. Target color and/or reflectivity don't affect ultrasonic sensors, allowing them to operate reliably in high-glare environments. Ultrasonic sensors are also a great solution for clear object detection and for liquid level measurement.
When Should I Use an Industrial Ultrasonic Sensor Instead of an Optical Sensor or Radar Sensor?
Ultrasonic sensors offer advantages when sensing clear objects, liquid level or highly reflective or metallic surfaces. Ultrasonic sensors also function well in wet environments whereas an optical beam may refract off the water droplets. However, ultrasonic sensors can be susceptible to temperature fluctuations or wind, things that don’t affect radar sensors. With optical sensors, you can also have a small spot size, fast response, and in some instances, you can project a visible spot on a target to help with sensor alignment.
How Do Ultrasonic Sensors Deal with Noise and Interference?
Because ultrasonic sensors use sound waves, any acoustic noise at the same frequency as the ultrasonic sensor uses may interfere with the sensor's output. This includes high-pitched noises such as those created by a whistle, and the hissing of relief valves, compressed air, or pneumatic devices. You may also experience acoustical crosstalk by placing two ultrasonic sensors of the same frequency close together. Electromagnetic devices create an alternating flow of electrons which makes vibrations. These vibrations can be picked up by electrical devices such as transformers, which create a hum that can interfere with ultrasonic sensors.
What Environmental Conditions Affect an Industrial Ultrasonic Sensor?
Temperature fluctuation affects the speed of an ultrasonic sensor's sound waves. As temperature increases, the sound waves travel faster to and from the target. While the target may not have shifted, the sensor may pinpoint the target as being closer. To solve this temperature problem, many of Banner’s ultrasonic sensors, including the T30UX Series and QS18U Series, compensate for temperature fluctuations to deliver high-accuracy performance across a wide range of ambient temperatures. Air currents caused by pneumatic equipment or fans may also deflect or disturb the path of the ultrasonic wave. This could lead a sensor to fail to recognize the correct location of a target.
Why Do I Need to Let My Ultrasonic Sensor Warm Up before I Operate It?
When a sensor is first powered up, the individual components heat up and also heat the surrounding space and components. This fluctuation in temperature from a cold start to the operating temperature is called "warm-up drift." Until all components have reached the correct operating temperature, the accuracy of measurements may be affected.
What Is a Dead Zone?
A dead zone refers to the area directly in front of the transducer face where the sensor cannot reliably make measurements. This is due to a phenomenon called ringing. Ringing is the continued vibration of the transducer after the sound wave, or excitation pulse, is sent. The energy must dissipate before the transducer can listen for a return echo. Because of this, targets should be located beyond the specified dead zone of an ultrasonic sensor. Some ultrasonic sensors, including Banner’s S18U Series, have a minimal dead zone and/or have the ability to eliminate the dead zone when used in retrosonic mode.
Are Ultrasonic Sensors Slower than Photoelectric Sensors?
In short, yes. The speed of sound is considerably slower than the speed of light. Therefore, an ultrasonic sensor, by its very nature, will be slower than an optical sensor.
What Are the Best Types of Targets for Use with an Ultrasonic Sensor?
The best targets for use with an ultrasonic sensor are large, flat, solid surfaces of materials such as metal, ceramic, glass, or wood. They should always be placed perpendicular to the sensor. Soft or irregular surface targets, such as pellets, sawdust, or foam are not detected effectively, and are better served by other types of sensors.
What Is the Best Way to Detect Randomly Placed Objects Using an Ultrasonic Sensor?
When setting up an ultrasonic sensor, teach the sensor the "background" as your good condition. By teaching an ultrasonically reflective background surface as the good condition, any object that is positioned between the sensor and the background will be detected, therefore causing the output to switch.
For more information about how precision measurement with ultrasonic sensors from Banner Engineering can improve your operations, contact a Banner engineer today.