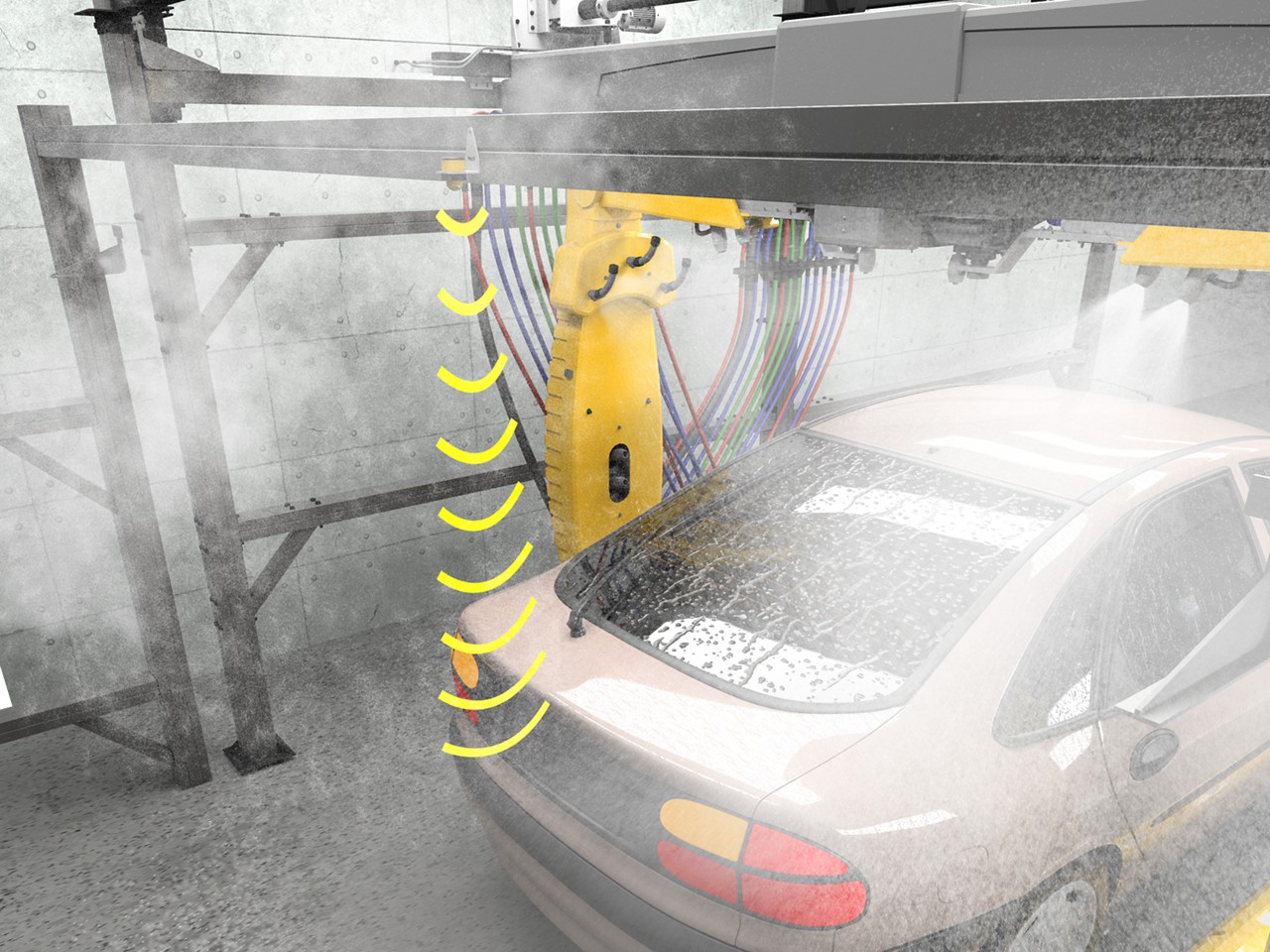
Get to Know Different Photoelectric Sensing Modes
Photoelectric sensors, which recognize a light source and convert received photons into an electrical signal, are one of the most common and fundamental sensor types. They have a long history in the development of modern technology, and they are indispensable in industrial automation. To select the right sensor for a given task, it’s important to understand the ways in which photoelectric (PE) sensors operate. These methods are called sensing modes.
Opposed Mode
In opposed-mode sensing, the sensor’s emitter and receiver are housed in two separate units. The emitter is placed opposite the receiver, so that the light beam goes directly from the emitter to the receiver. An object is detected when it “breaks” or interrupts the working part of the light beam, known as the effective beam. Depending on the application, opposed-mode sensing provides the highest reliability whenever it can be implemented. This is because light passes directly from the emitter to the receiver. Then, when an object breaks the beam, the output will switch.
Opposed-mode sensors offer the following advantages:
- The highest level of excess gain (emitted energy)
- A long sensing range
- The most robust option for harsh environments
- Precise position sensing
- Excellent detection of small parts, with the use of lens apertures
- Immunity to surface reflectivity (the color or finish of objects)
Retroreflective Mode
A retroreflective sensor contains both the emitter and receiver elements in the same housing. It uses a reflector to bounce the emitted light back to the receiver. Similar to an opposed-mode sensor, it senses objects when they interrupt or “break” the effective beam. Because retroreflective sensing is a beam-break mode, it’s generally not dependent upon the reflectivity of the object to be detected. However, if the objects passing by the beam are particularly shiny, a polarized retroreflective sensor should be used instead, to prevent proxing. Proxing is when an object with a shiny surface returns enough light to the sensor to mimic the photoelectric beam coming back from the reflector. A polarized retroreflective sensor uses a polarizing filter to ensure that the light returning to the receiver is coming from the reflector and not the target.
A retroreflective sensor offers a convenient alternative to opposed mode when space is limited, or if electrical connections are only possible on one side of a conveyor or other production pathway.
Retroreflective sensors offer the following advantages:
- Relatively long ranges
- The second-highest excess gain (after opposed mode)
- Proxing prevention using a polarized filter
- High detection precision and the ability to detect clear objects, using coaxial optics
Proximity Mode
As with many retroreflective sensors, a proximity sensor typically includes both an emitter and a receiver within the same physical housing. But while both opposed and retroreflective modes work by indicating an object’s presence when a beam is interrupted, proximity-mode sensors work in the opposite way, indicating a target object’s presence only when the beam reflects off it and returns to the receiver. One way to think about it: opposed and retroreflective sensors detect objects that break a beam, but proximity sensors detect objects that make a beam. There are four subtypes of proximity mode, each with a different optical arrangement: diffuse, divergent beam, convergent beam, and background suppression.
Diffuse sensors are the most common, and they receive light directly reflected from an object’s surface, often with the help of a lens. Diffuse proximity sensors offer the benefits of not requiring a reflector and being easy to install, generally for applications in which opposed mode or retroreflective sensors can’t be easily implemented or aligned. However, they tend to return a smaller amount of light (signal loss) and work best at shorter distances than opposed and retroreflective sensors.
Divergent-beam proximity sensors don’t use a lens. They’re less dependent on precise beam angles, but they’re best limited to applications to detect very small targets, such as wire or yarn, at extremely close distances consistently within one inch of the sensor.
By contrast, convergent-beam proximity sensors use lenses to focus both the emitted light and the receiver to the same exact point. This creates a small, well-defined sensing area at a fixed distance from the sensor. They can detect objects of very low reflectivity and ignore targets beyond their depth of field, making them useful for precise positioning of small parts. (One important caveat is that convergent-beam sensors can potentially detect brighter objects beyond their focal point. This aspect has led to an increased market for fixed- or adjustable-field background-suppression sensors, as described in the next bullet point.)
As their name implies, background-suppression proximity sensors ignore anything past a set cutoff. They work by comparing the amount of light returned to two separate receiver elements. Whenever a background suppression’s second receiver registers an equal or greater amount of light than its first receiver, it recognizes a target. Whenever the amount of light received by the first receiver is greater, the sensor’s output signal is cancelled. Background suppression sensors can be useful if objects you want to detect are darker than the background behind them (for example, dark object on a white conveyor belt). Background suppression sensors are available in fixed-field modes, which have a consistent cutoff distance, and adjustable-field modes, which allow users to set the cutoff.