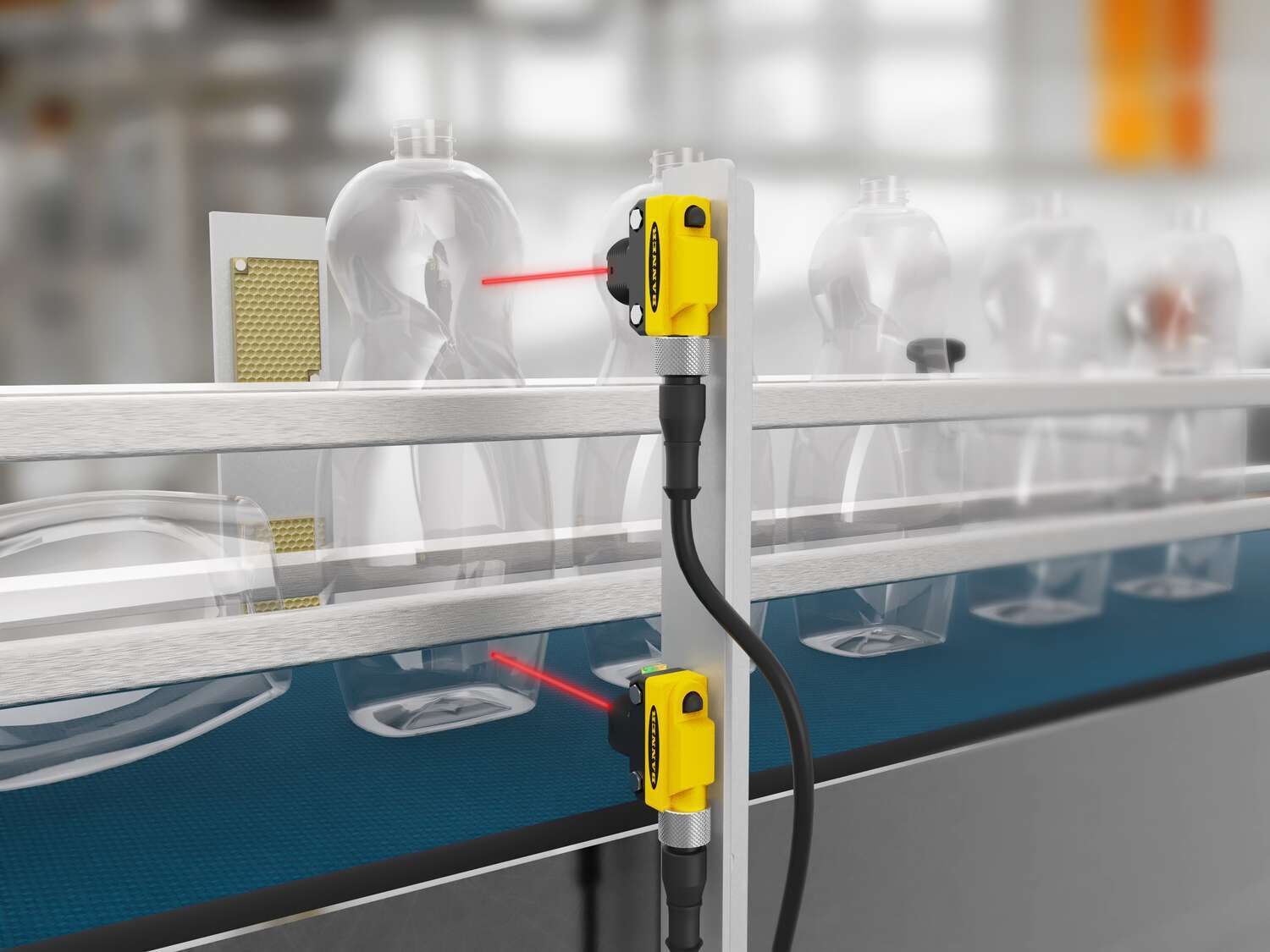
광전 센서
Banner는 전 세계에서 가장 완벽한 광전 센서 라인을 제공하며, Fortune 500에 이름을 올린 거의 모든 제조업체에 센서를 공급하고 있습니다.
When the light beam emitted by a photoelectric sensor is interrupted or reflected by the object, the change in light patterns is measured by a receiver and the target object or surface is recognized. Photoelectric sensors are very common in industrial manufacturing fields such as material handling, packaging, food and beverage, medical, and many others.
Depending on the style selected, they can be used with or without a reflector, be self-contained, long-range, heavy-duty, or compact. There are many different housing and mounting options to offer a correct fit that meets the demands of each application. They perform a wide variety of tasks and some of them can even be used in harsh environments.
포토 아이 센서라고도 하는 광전 센서는 항목 및 장비의 존재 여부 또는 표면 상태의 변화를 감지하는 데 사용되는 광선을 방출합니다. 방출된 광선이 물체에 의해 차단 또는 반사되면 수신기가 광 패턴의 변화를 측정하고 대상 물체 또는 표면을 인식합니다. 광전 센서는 재료 운반, 포장, 식음료, 의료 등과 같은 여러 산업용 제조 현장에서 매우 폭넓게 사용되고 있습니다.
선택한 스타일에 따라 반사 장치와 함께 또는 반사 장치 없이 사용할 수 있으며, 추가 장치가 필요 없거나, 범위가 길거나, 매우 견고하거나, 크기가 작을 수 있습니다. 여러 가지 다양한 하우징 및 장착 옵션이 있으므로 각 응용 분야의 요건에 적합하게 장착할 수 있습니다. 광전 센서는 광범위한 작업을 실행하며 그 중 일부는 혹독한 환경에서도 문제없이 사용할 수 있습니다.
Series Image | Series Name | Opposed Range (m) | Non-polarized Retroreflective Range (m) | Polarized Retroreflective Range (m) | Laser Polarized Retroreflective Range (m) | Diffuse Range (mm) | Fixed-Field Range (mm) | Adjustable-Field Range (mm) | Type of Emitter | Housing Material | IP Rating | Response Time (μs) | Operating Temperature | IO-Link | Clear Object Detection |
---|---|---|---|---|---|---|---|---|---|---|---|---|---|---|---|
Series Image |
Series Name QS18 | Opposed Range (m) 20 | Non-polarized Retroreflective Range (m) 6.5 | Polarized Retroreflective Range (m) 3.5 | Laser Polarized Retroreflective Range (m) 10 | Diffuse Range (mm) 600 | Fixed-Field Range (mm) 200 | Adjustable-Field Range (mm) 350 | Type of Emitter LED and Laser | Housing Material Plastic | IP Rating IP67 | Response Time (μs) 600–800 | Operating Temperature -20 to +70 °C | IO-Link ✅ YES | Clear Object Detection ✅ YES |
Series Image |
Series Name Q20 | Opposed Range (m) 20 | Non-polarized Retroreflective Range (m) 6 | Polarized Retroreflective Range (m) 4 | Laser Polarized Retroreflective Range (m) — | Diffuse Range (mm) 1500 | Fixed-Field Range (mm) 150 | Adjustable-Field Range (mm) 400 | Type of Emitter LED | Housing Material Plastic | IP Rating IP67 | Response Time (μs) 850–1000 | Operating Temperature -20 to +60 °C | IO-Link ✅ YES | Clear Object Detection 🚫 NO |
Series Image |
Series Name QS30 | Opposed Range (m) 60 | Non-polarized Retroreflective Range (m) 12 | Polarized Retroreflective Range (m) 8 | Laser Polarized Retroreflective Range (m) 18 | Diffuse Range (mm) 1400 | Fixed-Field Range (mm) 600 | Adjustable-Field Range (mm) 600 | Type of Emitter LED and Laser | Housing Material Plastic | IP Rating IP67 | Response Time (μs) 2000–5000 | Operating Temperature -20 to +70 °C | IO-Link 🚫 NO | Clear Object Detection ✅ YES |
Series Image |
Series Name T18-2 | Opposed Range (m) 25 | Non-polarized Retroreflective Range (m) — | Polarized Retroreflective Range (m) 6 | Laser Polarized Retroreflective Range (m) — | Diffuse Range (mm) 750 | Fixed-Field Range (mm) 200 | Adjustable-Field Range (mm) — | Type of Emitter LED | Housing Material Plastic | IP Rating IP67, IP68, IP69K | Response Time (μs) 1500–2000 | Operating Temperature -40 to +70 °C | IO-Link 🚫 NO | Clear Object Detection 🚫 NO |
Series Image |
Series Name Q3X | Opposed Range (m) — | Non-polarized Retroreflective Range (m) — | Polarized Retroreflective Range (m) — | Laser Polarized Retroreflective Range (m) — | Diffuse Range (mm) 300 | Fixed-Field Range (mm) 200 | Adjustable-Field Range (mm) — | Type of Emitter Laser | Housing Material Metal | IP Rating IP67, IP68, IP69K | Response Time (μs) 250 | Operating Temperature -10 to +50 °C | IO-Link 🚫 NO | Clear Object Detection 🚫 NO |
Series Image |
Series Name Q2X | Opposed Range (m) 3 | Non-polarized Retroreflective Range (m) — | Polarized Retroreflective Range (m) 3.3 | Laser Polarized Retroreflective Range (m) — | Diffuse Range (mm) — | Fixed-Field Range (mm) 50 | Adjustable-Field Range (mm) 3000 | Type of Emitter LED and Laser | Housing Material Plastic | IP Rating IP67 | Response Time (μs) 600–100,000 | Operating Temperature -25 to +50 °C | IO-Link ✅ YES | Clear Object Detection ✅ YES |
Photoelectric sensors can detect the presence or absence of objects or changes in surface conditions of a target. They emit a beam of light that is detected by a receiving element. When an object interrupts or reflects the emitted light, an output switches, sending an electronic signal. Most target materials can be detected including those that are shiny, dark, clear, or multicolored. Photoelectric sensors are very common in industrial manufacturing fields such as material handling, packaging, food and beverage, medical, and many others.
Photoelectric sensors can be long range, heavy duty, and compact, and they are available in various detection ranges. Some require separate emitters and receivers, others include both an emitter and a receiver in one housing (with or without a reflector), and some sensors are capable of differentiating targets from backgrounds. These various detection methods are known as sensing modes. There are many different housing and mounting options to offer a correct fit that meets the demands of each application. They perform a wide variety of tasks, can have a very fast response, and some can even be used in harsh environments.
Different applications require different approaches to sensing. To satisfy these diverse application needs, Banner offers multiple sensing modes including opposed, retroreflective, diffuse, and background suppression. The range at which detection occurs, the physical composition of the object being detected, and the environment in which the sensors operate can all affect the sensing mode choice.
In opposed-mode sensing, the sensor's emitter and receiver are housed in two separate units. The emitter is placed opposite the receiver, so that the light beam goes directly from the emitter to the receiver. An object is detected when it "breaks" or interrupts the working part of the light beam, known as the effective beam. Depending on the application, opposed mode sensing provides the highest reliability whenever it can be implemented. This is because light passes directly from the emitter to the receiver. Then, when an object breaks the beam, the output will switch.
- Opposed-mode sensing offers the highest level of excess gain (sensing energy)
- Long sensing range
- Most robust for harsh environments
- Precise position sensing
- Small-part detection using lens apertures
- Impervious to surface reflectivity (the color or finish of the object)
A retroreflective sensor contains both the emitter and receiver elements in the same housing. It uses a reflector to bounce the emitted light back to the receiver. Similar to an opposed-mode sensor, it senses objects when they interrupt or "break" the effective beam. Because retroreflective sensing is a beam-break mode, it is generally not dependent upon the reflectivity of the object to be detected.
However, it can be tricked by shiny objects. For those targets, a polarized retroreflective sensor should be used to prevent proxing. Proxing is when an object with a shiny surface returns enough light to the sensor to mimic the photoelectric beam coming back from the reflector and causes the object to not be detected. In a polarized retroreflective sensor, the emitter sends light waves through a filter that aligns them on the same plane. These light waves bounce off the reflector, and return to a vertically polarized filter on the receiver. When this polarized light reaches a shiny target, the light is reflected back to the sensor on the same plane as it was emitted and is blocked by the filter, signaling a broken beam. When the polarized light hits the reflector, however, it is scattered into unpolarized light with light waves on both the horizontal and vertical planes. Some of this light will pass through the receiver’s filter and the sensor will detect the reflector and know the beam is unbroken.
A retroreflective-mode sensor offers a convenient alternative to opposed mode when space is limited, or if electrical connections are only possible one side of the installation. Retroreflective-mode sensors offer relatively long ranges.
- Second-highest excess gain mode
- Polarized model available to prevent the beam from proxing off shiny objects
- Coaxial optics available for clear objects and precision
Diffuse-mode sensors contain the emitter and receiver in the same housing but do not use a reflector. Instead, they detect an object when emitted light is reflected off a target and back to the sensor. With a diffuse-mode sensor, the object is detected when it "makes" the beam; that is, the object reflects the transmitted light energy back to the sensor. They are significantly affected by the reflectivity of the target objects, which can drastically shorten their range. These sensors should not be used in applications with very small parts that need to be detected, in parts-counting applications, or where a reflective background is close to the object to be sensed. Diffuse-mode sensors are very convenient and are often used when opposed or retroreflective-mode sensors aren't practical.
- Low installation effort
- Does not require a reflector
The high excess gain of the adjustable-field Q2X allows it to reliably detect dark wafers. The tight minimum object separation can trigger the machine to move the next wafer into position as soon as the previous one is out of the way. And the small form factor easily fits into the machine without getting in the way.
- Simplify installation with fewer components and less wiring; no retro target or receiver required
- Ignore objects in the background with an adjustable cutoff distance between 18 mm and 150 mm
- Detect dark and challenging targets using powerful emitters with high excess gain
- Detect precise features with the small, bright-red LED or Class 1 laser emitter
- Avoid crosstalk when mounting multiple sensors in close proximity due to the advanced crosstalk immunity algorithm
Background-suppression (BGS) sensors are a diffuse-type sensor with a defined limit to their sensing range, ignoring any objects that lie beyond that range. There are two types of background-suppression sensors: fixed-field and adjustable-field. Both types use triangulation to determine the cutoff distance which allows the sensor to ignore anything beyond that point. The available excess gain inside the fixed sensing field is usually high, allowing sensing of less-reflective surfaces. A background-suppression sensor can often detect a dark target on a white background, as long as the background is past the sensor’s cutoff.
- Detects objects out to a set sensing distance
- Ignores background objects
- Very low color sensitivity
Excess gain is a measurement of the amount of light energy that the receiver element detects. A sensor needs an excess gain of one to cause the sensor's output to switch "on" or "off." However, contaminants in the sensing environment such as dirt, dust, smoke, and moisture can cause signal attenuation, so more excess gain will be required to receive a valid signal. Excess gain may be seen as the extra sensing energy available to overcome that attenuation.
An excess gain chart shows how much light energy is available at a given distance. The dirtier the environment, the more excess gain will be needed to overcome it. The graphs are logarithmic, which allows for a concise overview of data that varies by several orders of magnitude. Each minor tick increases by a factor of 1, and each major tick increases by a factor of 10. For example, starting at the origin and moving up the Y-axis, the graph's ticks represent 1, 2, 3, etc. Once the tick gets to 10, the ticks represent 10, 20, 30, etc. When the tick gets to 100, then the ticks represent 100, 200, 300, and so on.
Photoelectric sensors are available with a variety of sensing beams including visible LEDs, infrared LEDs, long wavelength infrared LEDs, and lasers, each of which has its benefits. Because applications are rarely the same, the choice of beam type and pattern will vary from one to the next. Banner offers an extensive line of photoelectric sensors to solve even the most challenging sensing requirements.
Visible LEDs
Visible LEDs help in the alignment and setup of a sensor, since the visible beam will provide a spot on the target. Red is the most common color for photoelectric sensors, because red diodes are inexpensive to make and the photodetectors in receivers are very sensitive to red light.
Materials will act differently to different wavelengths of light. A certain material may absorb one wavelength of light while reflecting another, or the contrast between two colors is low. In these cases, trying a different color LED, such as blue, can be a simple solution to the problem.
Infrared LEDs
Infrared (IR) LEDs are invisible to the human eye but are very efficient at producing light. This efficiency can help IR sensors see farther than visible LEDs. However, because the beam is invisible, it can make alignment more difficult.
Long-Wavelength Infrared LEDs
Typically, photoelectric sensors cannot see water because it is transparent to light in the visible spectrum. Fortunately, water efficiently absorbs the specific wavelength of 1450 nm, allowing for detection. Certain Banner sensors utilize long-wavelength infrared (LIR) LEDs operating at 1450 nm to detect liquids that contain water, while ignoring (burning through) clear or opaque containers.
Laser
Many Banner sensors use lasers for their emitted beams. Lasers use a small beam spot, delivering higher precision that is ideal for detecting very small objects or features. This beam remains very tight even over great distances, delivering precision detection at longer range.
The beam pattern represents the boundary within which the sensor will respond to a target. In opposed mode, the receiver can be anywhere within this pattern and will detect light from the emitter. In retroreflective mode, the beam pattern is dependent on the reflector being used. A smaller reflector will reflect less light, which results in a shorter range and a more narrow beam pattern. In diffuse mode, the target must be within the beam pattern to be detected. In diffuse mode, the beam pattern is created using a 90% white card, so different-colored targets will affect the beam pattern.
Sensors also have an effective beam, which is the “working” part of the light beam stretching from the emitter to the receiver. An object is detected when it breaks the effective beam. In opposed mode, the effective beam is established between the emitter and receiver. In retroreflective mode, because the emitter and receiver are housed in a single unit, the effective beam is established between the emitter, reflector, and receiver.
Photoelectric Applications
-
Accurate Positioning in Medical & Scientific Laboratories
-
Dark Wafer Presence Detection
-
Streamline Labeling Process with a Fixed-Field Sensor
-
Preventing Jams in Airport Baggage Retrieval Systems
-
Status Indication on Airport Conveyor
-
Positioning Pallets for Unloading by Robot Arms
-
지게차 안내 조명
-
Jam Detection on a Conveyor with Only AC Power
-
컨베이어 기계를 통과하는 투명 플라스틱 병의 일관적인 감지
-
작업자 안내 솔루션
-
고속 수축 슬리브 라벨 부착[성공 사례]
-
황색 병을 감지하는 청색 LED 센서 [성공 사례]
-
병 충전 수위 감지
-
카톤 더미 높이
-
수위 측정
-
개별 분리기에서 플라스틱 트레이 수위 모니터링
-
비접촉식 충전 수위 검증
-
QS30으로 판자 휨 감지
-
병 라벨 확인
-
정확한 포장을 위한 식품 상자 계수
-
날짜/로트 코드 인쇄를 위한 판지 상자 트리거
-
색상 정렬
-
컨베이어 걸림 감지
-
집적 회로 계수
-
메모리 스틱 계수
-
연장형 연결 컨베이어
-
물병의 충전 수위 확인
-
인쇄 시 검사 트리거
-
주스 상자 감지
-
QS18로 액체 유출 감지
-
Load Station Pallet Detection
-
우편물 크기 분류
-
충전을 위한 약병 감지
-
트레이 봉합 장치의 투명한 필름 모니터링
-
컨베이어 위의 물체
-
소포 충돌 방지
-
공급장치 보울에서 부품 감지
-
셔틀 토트 위치 선정
-
정렬 자동 유도 스테이션
-
금속 부품의 적재 높이 감지
-
호퍼 및 충전 스테이션에서 검은색 플라스틱 트레이 감지
-
병뚜껑 검사
-
제한된 면적에서 뚜껑 검사
-
캡 방향 확인
-
검은색 도어 패널에서 검은색 부품 감지
-
다양한 색상의 병뚜껑 감지
-
다중 벨트 컨베이어의 냉장 조식 롤 감지
-
뚜껑의 방향 감지
-
포켓 테이프에 로드된 집적 회로 칩의 오류 방지
-
포장 냉동 정식의 덮개 감지
-
부품이 제자리에 있는지 확인
-
엔진 블록의 고무 와셔 감지
-
나사산 구멍 감지
-
자동화된 임상 실험실을 통한 약병 추적
-
고속 병입 라인에서 기울어진 병 감지
-
컨베이어에 있는 투명 플라스틱 용기 계수
-
식음료 스플래시 존을 위한 투명 유리 항아리 감지
-
반사 링 계수
-
컨베이어 위의 반사형 포장물 감지
-
제품 흐름을 조절하기 위해 PET 병 감지
-
까다로운 화학적 환경에서 유리병 감지를 위한 위생 센서
-
싱글 파일러에 인라인 누적
-
투명 포장에서 투명 액체 감지
-
장거리 특징점 탐지
-
수직형 충전 밀봉 기계 솔루션
-
수하물 취급
-
배경 억제 기능을 이용한 주사기 계수
-
컨베이어 위의 다양한 크기의 포장물 감지
-
유리 패널 감지
-
AC 전원 컨베이어 위의 물체 감지
-
모터 감지
-
음료수 캔 흐름 제어
-
조립 공정 중 PCB 조립체에서 접착제 감지
-
조립 라인의 근접 오류 방지
-
검정 오링 감지
-
하드 디스크 감지
-
포장 라인에서 빠진 초콜릿이 있는지 검사
-
라벨링 감지
-
확산 모드 레이저 센서로 포장 검사 이미지
-
공급 볼 레일 위 부품 검사
-
스탬핑 프레스에서 판금 확인
-
위생 환경에서 투명 플라스틱 식품 용기 감지
-
호퍼 식품 저장 장치에서 투명 트레이 감지
-
기울어진 병의 유무 감지 및 표시
-
개별 분리기(Denester)에서 투명 식품 트레이의 라인 압력 제어
-
어둡고 대비가 낮은 표적
-
세척 환경에서 투명 유리 및 플라스틱 PET 병 감지
-
세척 환경에서 투명 병 감지
-
상자 포장기에서 냉동 식품 포장
-
출구 활송 장치 걸림 표시
-
세차장
-
극한 환경의 자동 세차장 내 차량 위치
-
투명하고 반사가 심한 표적
-
투명한 약병의 정확한 계수
Resources
The latest Photoelectric Sensors Solutions brochure explores the many different types of Banner sensors and how to choose the right one for your application, whether it be object counting, quality control, object presence or absence, or other automation need.